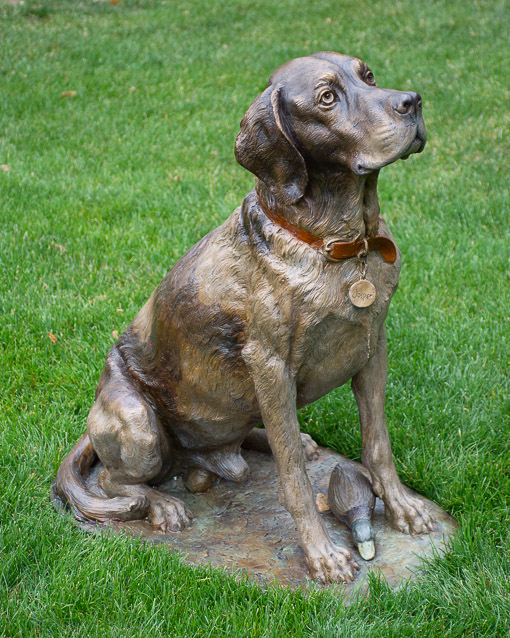
Exploring the
Bronze
Process
Below is an intro to bronze casting. The process is time intensive but the results are timeless. We hope you gain a appreciation not only for the artist’s work but appreciation for all the artisans that contribute.
Bronze casting dates back to the ancient Chinese and the process has largely remained unchanged for thousands of years. The sculptures are cast using the traditional lost-wax method. Today the process is improved by mechanized tools but the process remains the same.
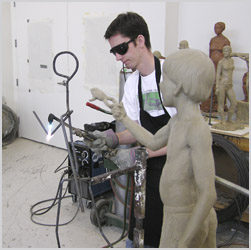
A Steel armature is fabricated that will function as a “skeleton” to hold the weight of the clay
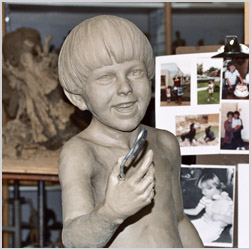
The piece is sculpted using an oil based clay
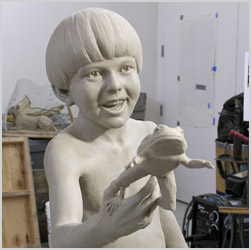
The piece is worked and reworked until both the artist and client are pleased
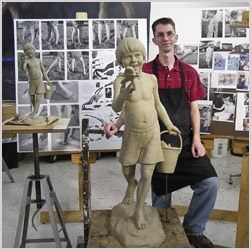
The finished life-size sculpture and small model
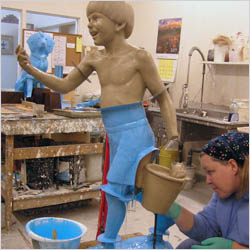
Thin sheets of metal are used to divide the sculpture in to a predetermined number of sections
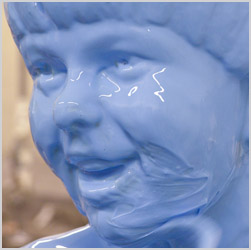
A latex rubber is applied to the clay sculpture. 5-6 coats are used to build up a sufficient thickness
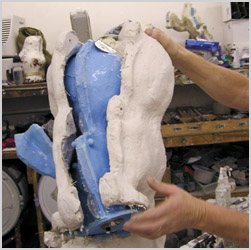
The molds are backed with plaster, which will give rigidity and support to the rubber
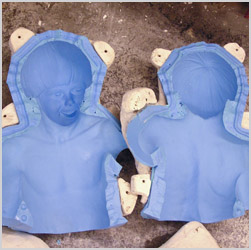
The plaster pieces are removed and the latex is cut down the center to create a two section mold
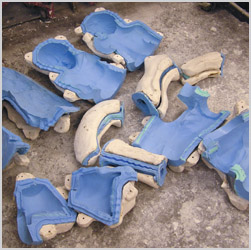
A finished set of Molds
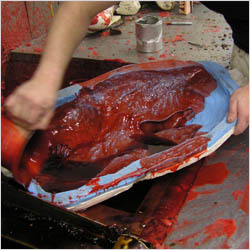
The molds are coated with wax to create a copy of the clay original
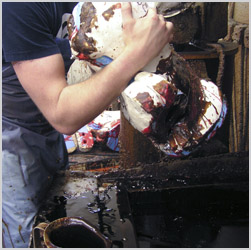
Wax is poured in, the mold is rotated to evenly coat, and the excess wax is poured out. This will create a hollow replica
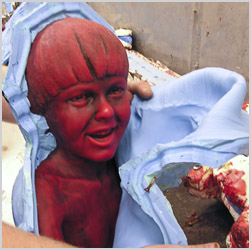
A finished wax being removed from the mold
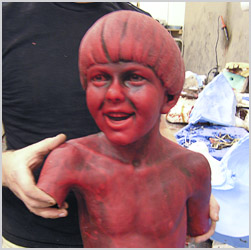
One finished wax piece
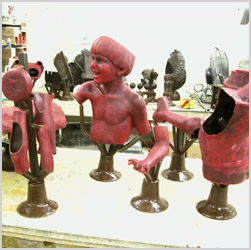
The pieces are touched up and wax runners and a wax cup are attached. The cup and runners will later act as funneling system to enable the bronze to reach the piece
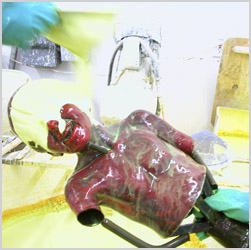
The pieces are coated in a liquid ceramic and allowed to dry. This will be repeated 7-8 times to build a thick ceramic shell. The shell becomes another mold
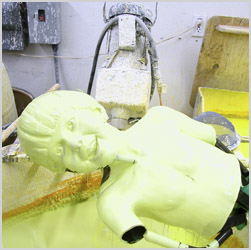
Finishing the first coat
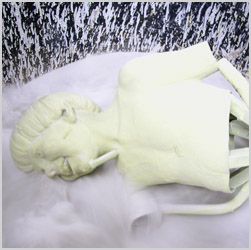
The piece is next coated in sand. This will help dry it quicker and add mass to the ceramic
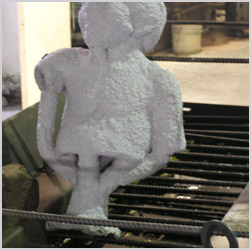
The ceramic is chipped away from the bottom of the cup gaining access to the wax. The piece is heated and the wax melts, leaving a hollow ceramic shell
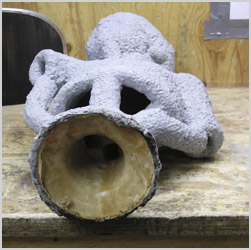
The mold is now hollow and ready for bronze to be poured in
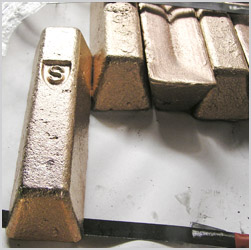
20 lbs. bronze ingots will be melted and poured into the shells
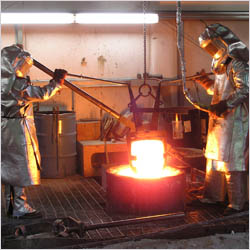
The bronze is melted in a crucible in a furnace to over 2000 degrees
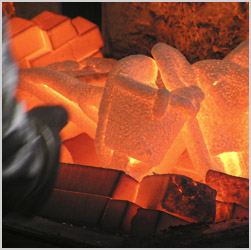
The ceramic shell are also heated, to prevent them from shattering from the shock of the molten bronze
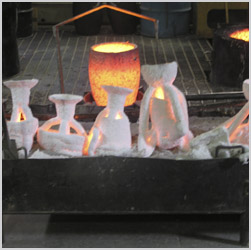
The shells are removed from the oven and placed in a sand filled box with the cup facing up
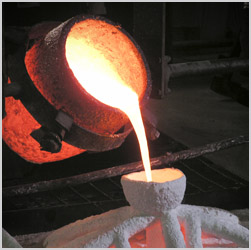
The cup acts as a funnel and the runners carry the bronze to the piece
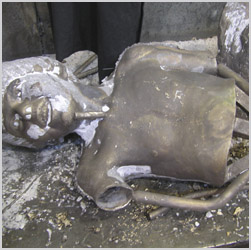
Once cooled, the ceramic shell is chipped away. Then the cup and runners will be cut off
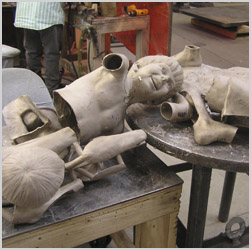
A finished set of bronze pieces ready to be reassembled
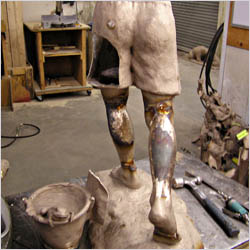
Using heli-arch welders the bronze pieces are welded back together. The sculpture is ground and polished to create a seamless finish
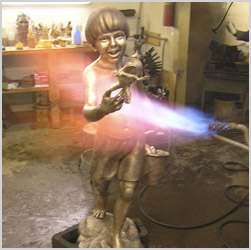
The sculpture is heated and treated with chemicals that oxidize the bronze changing its color to the desired effect
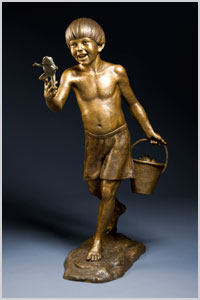
The finished piece is not only beautiful but strong and durable able to last generations!